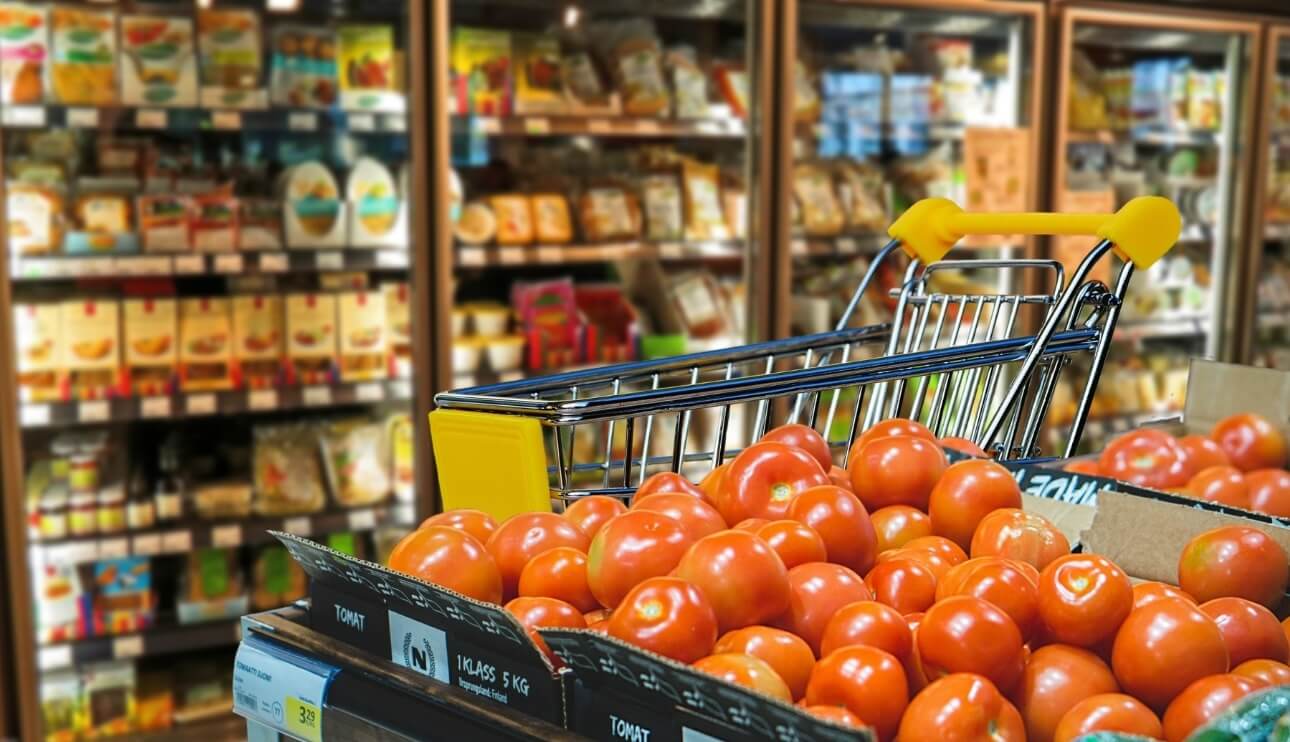
Technology is impacting almost every industry and the food service industry is no exception. The future of food service lies in remote monitoring, an innovation that is transforming the way retail operations are run.
With remote monitoring, foodservice operators can have real-time visibility into their operations from anywhere, at any time. By utilizing small, wireless sensors and the Internet of Things (IoT) technology, they can monitor everything from equipment performance to energy usage and food safety compliance.
This technology allows for proactive decision-making, minimizing downtime, optimizing resources, and improving overall efficiency. From preventing equipment breakdowns to ensuring food quality and safety, remote monitoring streamlines operations and enhances the customer experience.
Remote monitoring enables retailers to identify trends, anticipate demand, and make data-driven decisions to maximize profitability. With actionable insights at their fingertips, businesses can proactively adapt to changing conditions and deliver exceptional service.
As the future of food service continues to unfold, remote monitoring is proving to be an indispensable tool for retailers looking to thrive in an increasingly competitive landscape. Embracing this technology is key to delighting both customers and shareholders alike.
Benefits of remote monitoring in retail operations
Remote monitoring offers a myriad of benefits for foodservice operators, simplifying the way they manage their retail operations. First, remote monitoring enhances food safety and compliance efforts. With the ability to monitor temperature, humidity, and other critical parameters in real-time, businesses can ensure that food products are stored and handled in accordance with industry regulations. This not only prevents foodborne illnesses but also safeguards the reputation of the business.
In addition to improving food safety, remote monitoring also helps businesses maintain equipment performance. By monitoring equipment health and performance metrics, such as energy usage and maintenance needs, operators can proactively address issues before they escalate into costly breakdowns. This not only saves money on repairs but also minimizes downtime, ensuring smooth operations and uninterrupted customer service.
Remote monitoring improves food safety and compliance
Food safety and compliance are paramount in the food service industry, and remote monitoring plays a crucial role in ensuring adherence to regulations and standards. By utilizing wireless temperature sensors, businesses can monitor refrigeration units, freezers, and cooking equipment to ensure that food and medicine is stored or prepared at the appropriate temperatures.
In addition to temperature monitoring, remote monitoring systems can also track humidity levels, ensuring optimal conditions for food storage. This is particularly important for perishable items that require specific humidity levels to maintain freshness and quality.
Remote monitoring allows for continuous monitoring of critical control points, such as HACCP (Hazard Analysis and Critical Control Point) checkpoints. By automatically logging data and providing real-time alerts, businesses can quickly identify and address deviations from critical control points, preventing potential food safety risks.
“We just wrapped up a 3 day audit this morning…It went great! The auditor was impressed with OpSense. We love it.”
Alex Hernan, Yankee Trader Seafood
By enhancing food safety practices and compliance efforts, remote monitoring systems instill confidence in consumers, assuring them that the food and medicine they consume is safe and of the highest quality. This not only promotes customer loyalty but also protects businesses from potential legal and reputational risks.
Cost savings and efficiency gains
One of the key advantages of remote monitoring in retail operations is the potential for cost savings and efficiency gains. By having real-time visibility into operations, businesses can identify areas of waste and inefficiency, allowing them to make data-driven decisions to optimize resources.
For instance, remote monitoring can help businesses identify energy consumption patterns and highlight potential areas for energy savings. By monitoring energy usage in real-time, businesses can detect anomalies and take corrective actions, reducing energy waste and lowering utility costs. A recent study running over six months revealed that increasing the cold storage standard by just 3 degrees could reduce freezer energy consumption by more than 10% without any noticeable impact on product safety, texture, taste or nutrition of frozen food products.
“OpSense provides our team with visibility into all our locations. We have been able to reduce our energy consumption and save inventory.”
Summer Auerbach, Rainbow Foods
Remote monitoring also enables predictive maintenance. By continuously monitoring equipment performance metrics, businesses can identify early signs of impending equipment failures and schedule proactive maintenance. This prevents costly breakdowns and the need for emergency repairs in the middle of the night, ultimately saving both time and money.
The ROI of remote monitoring systems
The cost savings and efficiency gains achieved through remote monitoring can quickly outweigh the initial investment, making it a worthwhile endeavor for foodservice operators. For example, by preventing equipment breakdowns and minimizing downtime, businesses can avoid revenue losses associated with interrupted operations.
“Yesterday OpSense saved me $10,000. We got an alert right before we closed. A compressor went out. We had to pull 10 frozen doors of seafood and meat. It was all saved.”
Jackie Lawrence, Mac’s Fresh Market
Remote monitoring enables businesses to make data-driven decisions that maximize profitability. By identifying trends, predicting demand, and making informed pricing and purchasing decisions, businesses can optimize sales and margins. This leads to increased revenue and improved financial performance.
The enhanced food safety and compliance capabilities provided by remote monitoring systems can protect businesses from costly legal and reputational risks. By avoiding foodborne illnesses and maintaining a stellar reputation, businesses can attract more customers and secure long-term success.
Successful implementations of remote monitoring
To illustrate the effectiveness of remote monitoring in the food service industry, let’s explore a couple case studies of successful implementation. There are many more on our website that highlight results ranging from higher margins and operational excellence, to elevated staff efficiency and improved customer experience. Users benefit from reduced spoilage and lost inventory to equipment maintenance and repair savings, regulatory compliance and improved product quality.
B&R Stores
B&R Stores is an employee-owned corporation with 32 stores in Nebraska, Iowa and Missouri. Sustainability is a part of their mission along with delighting their customers and providing a quality shopping experience. They knew that they were losing product and therefore money and needed better refrigeration monitoring.
Just a week after installing OpSense one of the stores saved thousands of dollars in ice cream from a notification that the temperatures were too warm. The remote monitoring system provided real-time alerts for deviations from critical control points, allowing the staff to take immediate corrective actions. This proactive approach not only ensured compliance with food safety regulations but also prevented potential foodborne illnesses.
One evening when the compressor alarm went off after OpSense was installed, the staff was able to quickly look at OpSense and pinpoint the cases that had issues. This information helped direct the refrigeration company to the exact area to fix and other team members didn’t need to be disrupted to pull product, saving time and money.
The OpSense Dashboard provides visibility into all 32 stores so B&R is able to monitor the temperatures in every case across all stores without actually having to travel to each location. In addition to being notified of when there is an issue, problems can be pinpointed and solved quickly.
Wakefern
Wakefern Food Corporation, based in Keasbey, New Jersey is the largest retailers’ cooperative group of supermarkets. They operate three perishables distribution centers in New Jersey that handle all the produce, seafood, meat, dairy, deli, and bakery products for about 400 stores on the East Coast.
They wanted to digitize Wakefern’s manual processes to be able to provide more detailed reports to government regulators during audits and to know what was going on in all of their buildings without being physically present.
Immediately after installing OpSense remote monitoring they saw the value. The real-time data meant not having to manually take temperatures and the checklists save employee time and simplifies regulatory compliance and audits.
The most valuable result has been the validation of their assumptions related to the impact of weather impacting the temperatures inside the warehouse from the data gathered in OpSense. From the data we have from OpSense, Wakefern realized they could do better in protecting the cold chain.
Wakefern revolutionized how they manage food safety and compliance in their distribution centers with OpSense.
The impact of remote monitoring on the future of food service
As the future of food service unfolds, remote monitoring is proving to be an indispensable tool for retailers looking to thrive in an increasingly competitive landscape. By providing real-time visibility into operations, enhancing food safety and compliance efforts, driving cost savings and efficiency gains, and delivering a strong ROI, remote monitoring is revolutionizing retail operations.
Embracing this transformative technology is key to delighting customers with fresh safe food. Foodservice operators who leverage remote monitoring systems will be able to make data-driven decisions, optimize resources, and deliver exceptional service. With the ability to proactively monitor and manage their operations, they can adapt to changing conditions, identify trends, and maximize profitability.
Download the OpSense solution brief or schedule a call to discuss your monitoring needs.